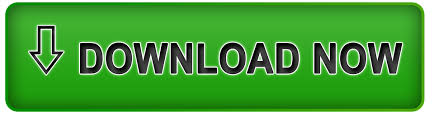

Understand how to setup a Flow Simulation project, get familiar with the user interface, prepare assemblies for fluid simulations, define boundary conditions, goals and other important parts of the project. SOLIDWORKS Flow Simulation can inform you about HVAC and electronics cooling, but it can also help warrior-engineer Johnny Snow keep dragons from roasting his soldiers alive – as you’ll see in the below trailer. Learn about SOLIDWORKS Flow Simulation, which enables anyone to simulate a wide range of real world problems involving dynamics of fluids. SOLIDWORKS Flow Simulation uses CFD to enable engineers and designers to quickly and efficiently simulate fluid flow and heat transfer – all directly inside of SOLIDWORKS 3D CAD.Īnd that brings us to the topic of dragons.

Your 3D CAD data that you created in SOLIDWORKS is the foundation and starting point for CFD analysis. The solidworks geometry of the wing was then saved in the format of stl as. When you need to understand how liquids and gases will flow through your design, you do not need to export information from SOLIDWORKS or get assistance from an expert. Thinking of foamyHexMesh as a meshing tool for air-flow simulations about a. The best way to stop a fire before it starts is by understanding computational fluid dynamics (CFD). Understanding how the flow of liquids or gases influences your design’s performance can be the difference between bringing a hot product to market and creating an unmitigated dumpster fire. Architecture, Engineering & Construction.This is how easy it is to solve complex Flow Simulation studies using the integrated technologies within the SOLIDWORKS Flow Simulation software. Using the built-in Flow simulation capabilities, SOLIDWORKS has optimized the indicator board in our example to the ideal dimension within the parameters we’ve specified. The results for our example are satisfactory, so we’ll click the green checkmark to exit the study manager. Fully embedded into SOLIDWORKS 3D CAD, the SOLIDWORKS Flow Simulation intuitive CFD (computational fluid dynamics) tool enables you to simulate liquid and. We can also create a new study from any of the design points, or go back and specify different minimum and maximum diameter values, run the study again, and see if we can optimize the design even further. We can also see a summary of the data in the parametric study pane.Īt this point, we can export the results as an excel file, just like in “What if?” mode, by clicking the “Export to Excel” icon. After the study has finished running, a dialogue box appears letting us know whether or not the results have converged.
SOLIDWORKS FLOW SIMULATION SOFTWARE
SOLIDWORKS Flow Simulation is a CFD software designed for the everyday. Why CFD Using simulation driven design with CFD gives you the tools to discover how air and liquids move in, through, and around your designs as well as und. Once we’ve defined the study options, we can click “Run” to start the study. Altair Hyperworks is a computational fluid dynamics software (CFD) suite that. Did you click the link in the email sent by SOLIDWORKS to. Did you create your SOLIDWORKS ID If not, create your ID now. Continue to create your ID Log in with your SOLIDWORKS ID. We’ll leave the rest of the options set to their defaults. Activate your account by clicking a validation link sent to your email. Keep in mind that if the number of calculations is too low, Flow may not have enough design points to find a solution that is close enough to the target value.įor our example, we’ll set the maximum number of iterations to 10. CFD SIMULATION WORK CAD modeling was done in Solidworks and fluid.

In the maximum number of calculations input box, we can define the maximum number of calculations or design points the study will calculate. The numerical solution will be conducted to predict the flow pattern by using. If we want to adjust any data in the scenario tab, we have to specify the study options. The scenario tab, located within the “Goal Optimization” mode, contains many of the same calculation options as it does in “What if?” mode, such as adding a computer to the project and the summary table rows and options.īut in our example, we can see that instead of having multiple design points, there is only one column of data and we can’t adjust any values using the summary table, like we can in “What if?” mode. In the scenario tab of the parametric study, we can easily adjust the study options to specify the finishing conditions, define the calculations before running the study and create a Flow Simulation project based on the results we obtain.
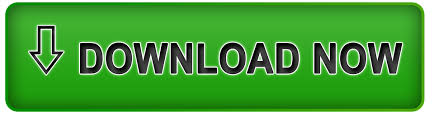